3KT浮標船A型架吊放系統安裝項目日前已在武船集團船舶公司全面展開。該系統整體重量約150多噸,結構復雜、零部件較多,安裝工藝精度要求近乎苛刻,是目前世界船舶制造領域安裝高度最高、安裝難度最大的海上工程裝備。
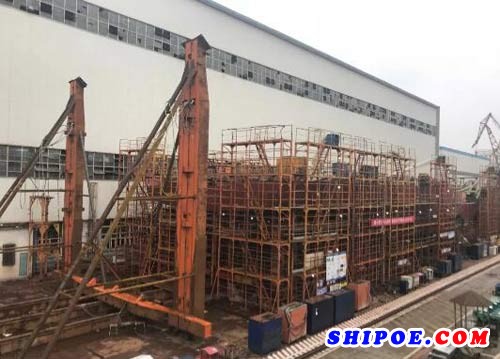
該系統主要零部件A架主體高22.9米、寬17.5米,相當于8層樓高;焊接在兩舷的A架基座平臺長約7米、寬約1米,焊接完成后,兩舷基座平面高度差需控制在2mm之內;長約17米的A架防蕩裝置軌道焊接完成后,還需確保1mm/3M的平面精度要求;船臺階段A型架吊放系統整體安裝報檢合格并不意味著項目結束,系泊試驗階段還需進行80T重的系統負荷試驗。
攻關過程
成立專項公關小組
船舶公司領導班子對此高度重視,項目啟動前組織成立了“A型架吊放系統安裝”專項攻關小組,自主編寫了該系統安裝項目施工方案,并繪制了A架支撐工裝平臺圖紙。由于該系統部件為國外散裝供貨,小組成員的首要任務便是確定A架的安裝方式。經過小組多次會議商討及風險評估、分析,并充分考慮到質量、安全、環境等多方面不確定綜合因素的影響,最終通過了分體式散件上船安裝A架的方案。
確定A架安裝平臺搭建方案
一波未平,一波又起。分體式安裝A架方案實施過程中,一方面要確保焊接在船體兩舷基座、軌道等平面安裝精度完全滿足工藝要求,另一方面要完備A架安裝時大型支撐工裝及施工作業平臺的搭建。依照供貨方提供的安裝數據要求,A架主體艉傾35°角進行安裝。船臺地面至產品主甲板平面高度約為10米,A架主體高約23米,并與主甲板平面呈35°夾角,以A架主體高度為三角斜邊數據,可以粗略估算出,小組需在船臺區域組織搭建約24米以上且十分穩定的現場施工平臺,才能確保該項目的安全開展。
方案實施
在初步確定了A架安裝平臺搭建方案后,小組成員迅速反應,對施工現場進行了實地勘測,并與設計、工藝、質量、安全等部門多方聯系,對每項措施進行評估評審,計算并反復校驗平臺搭建方案穩定性、安全性數據,充分調動公司現有一切資源,就地取材利用庫存材料制作各類輔助工裝,為保質保量按期安全完成A型架吊放系統船臺區域安裝項目奠定了堅實基礎。