近日,中國船舶集團(tuán)旗下江南造船正在建造的全球最大級別99000立方米乙烷運輸船(VLEC)上的2個超大B型液貨艙已完成主體建造和轉(zhuǎn)場,標(biāo)志著該公司B型艙建造取得重大突破,也為該系列首制船年內(nèi)交付打下堅實基礎(chǔ)。
全球首次應(yīng)用江南“BilliancE”B型艙技術(shù)
“BilliancE”B型艙由江南造船自行研發(fā)設(shè)計并擁有完全自主知識產(chǎn)權(quán),具有優(yōu)良的安全性、適用性和經(jīng)濟(jì)性。該型液艙也是全球首例應(yīng)用“BrilliancE”B型艙技術(shù)且大量使用鎳鋼薄板的B型艙。99000立方米VLEC船副總工藝師周清華介紹。
在系列船開工建造之初,江南造船組建了一支勇于打硬仗、敢于創(chuàng)新的B型艙專項攻關(guān)團(tuán)隊,經(jīng)過十余次周密的策劃與推演,梳理出近百項風(fēng)險點及應(yīng)對措施,通過對100余項試板、試驗件、模擬分段的建造工藝攻關(guān)與技術(shù)論證,攻克了B型艙鎳鋼高效焊、精度鏈、建造質(zhì)量控制等一系列關(guān)鍵技術(shù)。先后完成了分段建造、?總段總組、整艙合攏駁運、吊裝等多項專題策劃,并編制了《菱形液貨艙建造質(zhì)量標(biāo)準(zhǔn)》、《層壓木安裝與環(huán)氧澆注工藝》、《液貨艙建造與安裝作業(yè)指導(dǎo)書》等專項工藝、工法和作業(yè)指導(dǎo)書65份,為B型艙的節(jié)拍化建造做好了充足的準(zhǔn)備。
多措并舉保證產(chǎn)品質(zhì)量穩(wěn)定受控
“B型艙具有建造質(zhì)量要求高、裝配精度要求高等特點,我們采取了一系列針對性措施,確保了液艙分段的有序建造。”江南重工液艙總建造師蔣淮表示。江南重工作為目前唯一制作B型艙的生產(chǎn)單位,建造團(tuán)隊提前完成了詳細(xì)的生產(chǎn)準(zhǔn)備策劃和一系列嚴(yán)格的工藝指標(biāo)和操作規(guī)程;分階段對全體施工人員開展作業(yè)指導(dǎo)書工藝宣貫與培訓(xùn);對現(xiàn)有場地和人員重新進(jìn)行匹配分析、梳理劃分;經(jīng)過多項工法提升、工裝改進(jìn),保證安裝精度可控;推行智能焊接管控,對每一條焊縫分類分級管控,最終實現(xiàn)焊接一次拍片合格率超過97%。
超大件轉(zhuǎn)場再獲突破
根據(jù)生產(chǎn)總體要求,液艙將在室內(nèi)船臺完成絕緣敷設(shè)工程,如何將液艙從總組平臺順利轉(zhuǎn)場到室內(nèi)指定區(qū)域,這一艱巨的任務(wù)落在了經(jīng)驗豐富的大件駁運、吊裝技術(shù)創(chuàng)新工作室團(tuán)隊的身上。面對此次轉(zhuǎn)場,他們不敢掉以輕心。
“此次液艙轉(zhuǎn)場的難點在于盡可能的減少模塊車駁運受力點墩木的布置,在接近極限的空間內(nèi)要實現(xiàn)轉(zhuǎn)向,并順利進(jìn)入垮間,對我們來說極具挑戰(zhàn)。”搭載部副部長王國軍表示。與86000立方米液化氣船A型艙相比,B型艙在室內(nèi)船臺進(jìn)行絕緣敷設(shè)工作,墩木布置、模塊車駁運需要預(yù)留絕緣修補點作為頂升受力點,為減少后續(xù)修補,團(tuán)隊通過方案優(yōu)化,減少絕緣預(yù)留修補點50%以上,大幅提升絕緣敷設(shè)效率。此外,室內(nèi)船臺的東西兩側(cè)間距不足0.4米,江南大道的轉(zhuǎn)向操作空間不足10米。整個轉(zhuǎn)運好比螺螄殼里做道場。團(tuán)隊經(jīng)過精密測算、軟件模擬、實地勘驗,轉(zhuǎn)運過程中一邊行駛、一邊調(diào)整角度,最終在4天內(nèi)順利實現(xiàn)2個超大型液艙的轉(zhuǎn)場工作,將不可能完成的任務(wù)變?yōu)楝F(xiàn)實。
此外,江南造船在B型首艙建造中,高效焊技術(shù)應(yīng)用比例超75%,并形成了一套得到船東船檢認(rèn)可的專用建造質(zhì)量標(biāo)準(zhǔn),有力支撐了產(chǎn)品節(jié)拍化建造。接下來,VLEC項目團(tuán)隊將不斷奮進(jìn),以首創(chuàng)、敢拼的精神完成后續(xù)液艙建造,支撐公司在高端液化氣船市場的布局與長遠(yuǎn)發(fā)展。
全球首次應(yīng)用江南“BilliancE”B型艙技術(shù)
“BilliancE”B型艙由江南造船自行研發(fā)設(shè)計并擁有完全自主知識產(chǎn)權(quán),具有優(yōu)良的安全性、適用性和經(jīng)濟(jì)性。該型液艙也是全球首例應(yīng)用“BrilliancE”B型艙技術(shù)且大量使用鎳鋼薄板的B型艙。99000立方米VLEC船副總工藝師周清華介紹。
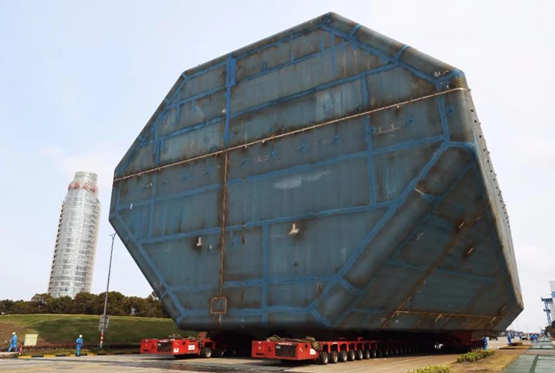
多措并舉保證產(chǎn)品質(zhì)量穩(wěn)定受控
“B型艙具有建造質(zhì)量要求高、裝配精度要求高等特點,我們采取了一系列針對性措施,確保了液艙分段的有序建造。”江南重工液艙總建造師蔣淮表示。江南重工作為目前唯一制作B型艙的生產(chǎn)單位,建造團(tuán)隊提前完成了詳細(xì)的生產(chǎn)準(zhǔn)備策劃和一系列嚴(yán)格的工藝指標(biāo)和操作規(guī)程;分階段對全體施工人員開展作業(yè)指導(dǎo)書工藝宣貫與培訓(xùn);對現(xiàn)有場地和人員重新進(jìn)行匹配分析、梳理劃分;經(jīng)過多項工法提升、工裝改進(jìn),保證安裝精度可控;推行智能焊接管控,對每一條焊縫分類分級管控,最終實現(xiàn)焊接一次拍片合格率超過97%。
超大件轉(zhuǎn)場再獲突破
根據(jù)生產(chǎn)總體要求,液艙將在室內(nèi)船臺完成絕緣敷設(shè)工程,如何將液艙從總組平臺順利轉(zhuǎn)場到室內(nèi)指定區(qū)域,這一艱巨的任務(wù)落在了經(jīng)驗豐富的大件駁運、吊裝技術(shù)創(chuàng)新工作室團(tuán)隊的身上。面對此次轉(zhuǎn)場,他們不敢掉以輕心。
“此次液艙轉(zhuǎn)場的難點在于盡可能的減少模塊車駁運受力點墩木的布置,在接近極限的空間內(nèi)要實現(xiàn)轉(zhuǎn)向,并順利進(jìn)入垮間,對我們來說極具挑戰(zhàn)。”搭載部副部長王國軍表示。與86000立方米液化氣船A型艙相比,B型艙在室內(nèi)船臺進(jìn)行絕緣敷設(shè)工作,墩木布置、模塊車駁運需要預(yù)留絕緣修補點作為頂升受力點,為減少后續(xù)修補,團(tuán)隊通過方案優(yōu)化,減少絕緣預(yù)留修補點50%以上,大幅提升絕緣敷設(shè)效率。此外,室內(nèi)船臺的東西兩側(cè)間距不足0.4米,江南大道的轉(zhuǎn)向操作空間不足10米。整個轉(zhuǎn)運好比螺螄殼里做道場。團(tuán)隊經(jīng)過精密測算、軟件模擬、實地勘驗,轉(zhuǎn)運過程中一邊行駛、一邊調(diào)整角度,最終在4天內(nèi)順利實現(xiàn)2個超大型液艙的轉(zhuǎn)場工作,將不可能完成的任務(wù)變?yōu)楝F(xiàn)實。
此外,江南造船在B型首艙建造中,高效焊技術(shù)應(yīng)用比例超75%,并形成了一套得到船東船檢認(rèn)可的專用建造質(zhì)量標(biāo)準(zhǔn),有力支撐了產(chǎn)品節(jié)拍化建造。接下來,VLEC項目團(tuán)隊將不斷奮進(jìn),以首創(chuàng)、敢拼的精神完成后續(xù)液艙建造,支撐公司在高端液化氣船市場的布局與長遠(yuǎn)發(fā)展。