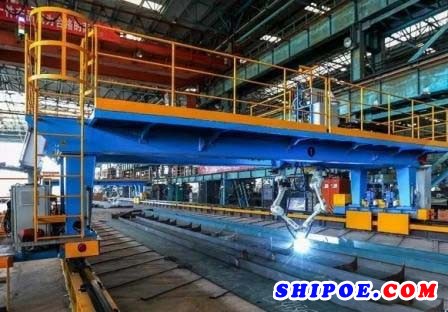
公司黨委書記、董事長陳建良接受訪談時表示,作為中國創造、創新的標桿企業,滬東中華將不斷加大船舶智能制造的投入,形成規模效應,提高分段制造效率,降低建造成本。并將持續推進智能制造在大型集裝箱船、集裝箱滾裝船等高附加值船上的運用。
LNG船數字化車間項目占地53000多平方米。服務于LNG船分段加工制造,對分段建造過程的數字化、管理的信息化、裝備的智能化展開研究,為LNG船大批量、高效率建造,創造了有利條件。車間內設置的iGPS高精度測量與檢驗系統,能較好提高制造精度與效率。
數字化車間的焊接機器人生產線,是目前最先進的國產化自動焊接系統,以設計數據及三維模型為基礎,實現分段小部件高質焊接。設備可24小時焊接,將員工從高強度的體力勞動中解脫出來,從而保持質量穩定。同時降低了對員工操作技術的要求,一定程度上解決了企業高技能人才緊缺的難題。